-
20th September 2021, 11:21 PM
#1
Trueblood 30-ton help needed
I acquired a Trueblood TB 30B-1.1 screw-type molding machine ... basically free except for the cost of trucking it to my home.
It is controlled by an Allan Bradley SLC-503 and an Allan Bradley 550 PanelView operators panel.
Part of my problem is that I have electrical and hydraulic diagrams but I do not know how the machine is supposed to act or how to set the operating parameters. I do not have a "setup" or "operator's" manual. I only have experience with a much older ram-type machine.
I know that it is designed to close the clamp at low speed, low pressure until it reaches a certain point (to check for obstructions) and after that build to full clamping force.
On the PanelView the screen for the clamp settings looks like this:
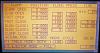
My understanding is that the "Min 10" in the upper right says that the hyd pump will be shut down if the machine has been idle for 10 minutes.
Note that the current "actual" position is -0.003. When this photo was taken, the clamp had fallen slowly as far down as it would go.
All positions referenced below (I assume) are distances "up" from this position. I don't know what the "Mach. Cycle 28.91" is other than perhaps what the calculated cycle time would be with these parameters?
All values below were in the machine but are suspect because the backup battery was down to 0.1 volts (from 3v) when I got the machine.
When I press manual "Clamp Open", I assume:
* "Clamp Open" is the final position (upper most) that the clamp will move to when I manually command it to open.
* "Slow Open" .. the clamp will open slowly after reaching this point during the open cycle to the final "Clamp Open" height using a flow rate of 90% and a pressure of 900 psi.
* "Fast Open" .. the clamp will open quickly after reaching this point during the open cycle to the final "Slow Open" height using a flow rate of 100% and a pressure of 1500 psi.
When I press manual "Clamp Close", I assume:
* The clamp will fall quickly using a flow of 100% and a pressure of 1500 psi for a maximum of 5 seconds to the "Slow Close1" position and fault if "Slow Close1" is not reached in that time (obstruction).
* After reaching "Slow Close1" it will close using 45% flow at 1000 psi to the "Slow Close2" position for a maximum of 16 seconds and fault if "Slow Close2" is not reached in that time (obstruction).
* After reaching "Slow Close2" it will close using 3% flow at 821 psi until it reaches the final close position of "Clamp Close". Note that the position shown (7.280") seems wrong because it is above Slow Close1. The flow and pressure could be right, I don't know.
* The current "Clamp Close" position does not seem correct in that it is only 0.020" from the maximum downward position and I doubt that a mold would have been this close to that dimension (BTW at the current position shown of -0.003, bottom of the stroke, the clamp is about 5.75" above the rotary table).
In my trials I have had the following symptoms of something going wrong:
* When I first try things in a session Clamp Open seems to work except that, if I hold it, the clamp seems to oscillate slowly about an inch at the top of the stroke. I assume that this is because the "counterbalance" check-valve on the Clamp valve body group is sticking open.
* If the clamp is at the top of its stroke and i release the Clamp Open buttons, the clamp slowly falls (about 1" per second). I take this as another indication that the counterbalance check-valve is not closing.
* If, while falling, I quickly press the Clamp Close buttons, the clamp will be driven down. After that, the Clamp Open seems to work better indicating to me that the counterbalance check-valve was forced to seat and/or become unstuck.
* If I hold the Clamp Close sufficiently long enough, the prefill valve closes and the clamp builds to a gauge pressure of 3,000 psi.
Do my assumptions above seem reasonable?
Is anyone familiar with Trueblood machines?
Are these parameters fairly standard to the industry?
Does anyone know where I can get a "setup" manual for this machine? I have searched the Internet but I can't find "Trueblood" (a division of PH Group) or a follow-on corporation I could contact for information.
Is it normal for the clamp to build to maximum clamping force even though it might not be needed for a given mold?
Does anyone know what Allan Bradley (now Rockwell) Rslogix software I can use to upload the SLC503 program to my PC? The latest version does not seem to understand SLC50x PLCs.
I have more questions but I'll stop there for now.
Thanks in advance for any guidance you might be able to offer. I can provide a hydraulic diagram if desired. I'm a retired EE by education but spent my whole work life in software development.
Regards,
Chuck Hackett
Last edited by Chuck H; 21st September 2021 at 12:45 AM.
Reason: correct picture
-
22nd September 2021, 08:43 AM
#2
Re: Trueblood 30-ton help needed
Hey Chuck,
Just looking at the panel pic it looks to me the slow close 1 and 2 positions are not correct, as the clamp is closing on fast close it will reach the slow close 1 position first then reach slow close 2 position before final clamp close. The positions settings on the panel are not in order. Also the settings for flow open and close are higher then normal, if these settings need to be this high to get movement then there maybe issues with the servo valve for flow control.
#2 Typically there is an adjustment to change Clamp high pressure settings for different mold sizes.
#3 I think the time shown in the right hand corner is the minimum amount of time allowed for the clamp to open before alarming it would be 10 seconds
#4 You are correct the -.003 is clamp fully closed position and increases as the clamp opens.
#5 If your clamp open stop setting is set too high reaching the fullest stroke of the clamp the oscillating issue you describe may be built into machine design to keep the clamp cylinder from crashing (hard Stop) when opening. Reduce the Open stop position setting and the clamp will stop before that decompression stage.
#6 Over the next couple days I will check on a source for additional true blood information. Including the software. They have or had 1 true blood.
-
23rd September 2021, 01:26 PM
#3
Re: Trueblood 30-ton help needed
Hi Bryan, thanks for the reply ...
***Just looking at the panel pic it looks to me the slow close 1 and 2 positions are not correct, as the clamp is closing on fast close it will reach the slow close 1 position first then reach slow close 2 position before final clamp close. The positions settings on the panel are not in order.
That was my thought (#1 & #2 reversed). I got the machine about 6 years ago (unknown how long it was out of service). When I finally got around to converting it from 480 3-phase to 240 3-phase (which I have here at the house) I discovered that the CMOS backup battery on the AB SLC503 was down to 0.1v from 3.0v and I think some/all of the setup info is suspect. Some seem reasonable, some totally weird. There are a total of 10 "recopies" that can be selected. All but this one (#1) show positions which cannot be reached (from what I gather, clamp position can be 0" to +8.5").
*** Also the settings for flow open and close are higher then normal, if these settings need to be this high to get movement then there maybe issues with the servo valve for flow control. #5 If your clamp open stop setting is set too high reaching the fullest stroke of the clamp the oscillating issue you describe may be built into machine design to keep the clamp cylinder from crashing (hard Stop) when opening. Reduce the Open stop position setting and the clamp will stop before that decompression stage.
I am currently trying to diagnose the reason that the clamp falls (about 1" per second) when not being driven and the reason it 'oscillates' at the top of the stroke - it also goes up 'jerkily' sometimes and falls when the hyd pump is turned off. I have studied the hydraulic diagram. There is a 'counterbalance' valve block in the valve stack which should prevent the clamp from falling when not being driven. As I see it, there are three things that could cause the clamp to fall/not hold position 1) relief valve in counterbalance valve leaking or set too low, 2) the check valve in counterbalance valve leaking, 3) the piston seal leaking. Given that the clamp falls at a significant rate, 1"-2" per second, when I turn off the pump my thought is that it's the piston seal because that's the thing most likely to have sufficient area to allow that much fluid to flow that fast.
BTW: The clamp has two cylinders, a smaller upper 'positioning' cylinders (1.5" bore) and a lower 'clamping' cylinder (5" bore) - i am dealing with the smaller one at the moment.
I have removed, cleaned and inspected the counterbalance valve body (with the limit check and normal check) and found nothing suspect. My plan is (with pump off) to raise the clamp to the top, place a support under it, seal off the lower cylinder port, crack open the upper port and then remove the support. If the clamp falls I know that it's the piston seal in the upper cylinder.
*** #2 Typically there is an adjustment to change Clamp high pressure settings for different mold sizes.
Still looking for this. I don't see a screen setting (checked all the screens) that seems to say something like "Final Clamp Pressure/force". I do have two manual reliefs. one for "Reduced Pressure" (~500 psi range) and "Injection Pressure" (~3000 range if i recall correctly). If I let the manual close cycle go far enough the clamp goes to full clamp and the clamp pressure gauge goes to 3,000.
*** #6 Over the next couple days I will check on a source for additional true blood information. Including the software. They have or had 1 true blood.[/QUOTE]
That would be GREAT ... or even the contact info for an operator who is familiar with the Trueblood.
Thanks again.
Chuck
(I must be doing something wrong. I get a server error when I try to use [QUOTE] [\QUOTE] tags)
-
23rd September 2021, 01:37 PM
#4
Re: Trueblood 30-ton help needed
Hyd diagram (left part of page) ... I am dealing with the "Jack Cylinder"
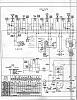
(Right part of page)
-
24th September 2021, 12:36 AM
#5
Re: Trueblood 30-ton help needed
Usually when the battery dies on the AB CPU, you will lose the entire PLC program, not only the setup. Also this is likely a retrofit job done by some previous company, just looking at photos on google they typically have a membrane keypad.
-
24th September 2021, 02:24 AM
#6
Re: Trueblood 30-ton help needed
*** Usually when the battery dies on the AB CPU, you will lose the entire PLC program, not only the setup. Also this is likely a retrofit job done by some previous company, just looking at photos on google they typically have a membrane keypad.
The program itself is definitely intact. I am not an expert on these (EE and Software developer), but my understanding is that the AB SLC503 could use EPROM or EEPROM (neither require battery backup) but the RAM (parameter storage and live variables) requires batter backup. So, if the EEPROM is used, the program isn't lost when the CMOS battery dies.
see: "https://literature.rockwellautomation.com/idc/groups/literature/documents/um/1747-um011_-en-p.pdf"
Yes, my panel (AB PanelView 550) has a membrane keyboard.
Chuck
-
26th September 2021, 10:29 PM
#7
Re: Trueblood 30-ton help needed
I made a bit more progress. I removed and cleaned the pressure relief and check valve that make up the "counter balance valve" (on left page above just under the "Clamp Motion" valve). Either I fixed it, or disassembly/reassembly of the valve stack fixed something because the clamp open/close motions have settled down and the clamp stays up when it should.
Playing with the parameters I discovered s set of settings that will successfully clamp down on an aluminum block (stand-in for a mold):
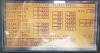
Close1 and Close2 seem backwards but when I reversed them (close1 > close2) I couldn't get it to work.
The 0.766 "actual pos" shown is the clamp closed onto the dummy mold.
Interestingly, earlier I was using a stack of wood 2x6 blocks as a dummy mold but was unsuccessful in getting it to hold clamp pressure. Turns out that I think it was detecting that, due to the compression of the wood, the ram moved when full (3,000) pressure was applied and aborted the closing. When I substituted aluminum it worked fine.
Now that the clamp is holding I have to finish the re-wiring of the heaters from 480 3-phase to 240 3-phase before I can test the heater and screw functions.
Still looking to talk to a Trueblood operator or lay my hands on Trueblood setup info.
Chuck
Posting Permissions
- You may not post new threads
- You may not post replies
- You may not post attachments
- You may not edit your posts
-
Forum Rules