-
2nd March 2020, 07:33 PM
#1
Re: 20% GF PP Warp
Possible to create a cooling fixture so that the parts cannot warp while cooling?
-
2nd March 2020, 07:47 PM
#2
Re: 20% GF PP Warp
The parts are already warped as soon as the robot drops it in the cage.
-
3rd March 2020, 08:47 AM
#3
Re: 20% GF PP Warp
PP TF is a solution or the tool must be adjusted to compensate warping.
I am prefering Mouldflow analyse before any changes.
-
3rd March 2020, 03:21 PM
#4
Re: 20% GF PP Warp
Is moving to a 20% glass bead filled PP an option?
-
5th March 2020, 01:39 AM
#5
Re: 20% GF PP Warp
What about melt temps? Entire mold hotter too? I only see on gate. Where are the others? I know this won’t run a decoupled process due to reminding me of plastic bowl lids; they look like potato chips when you mold them like you should. Since you have Valve gates I'd pack for a short time and shut them. Allowing the mold temp to lower the molded in stress and differential shrinkage. What’s the MF of the resin? Higher might help. Ask do they really need the glass fiber.
Rick
-
6th March 2020, 02:11 PM
#6
Re: 20% GF PP Warp
Sorry, to say but you may need to add some windage to the tool and it may be a little late - not sure.
Suhas
-
10th March 2020, 05:51 PM
#7
Re: 20% GF PP Warp
So again, we were able to convince the customer to switch to a talc reinforced material (TPO) on the seat back that I was having warp issues with. This will not always be a possibility, any tips for gating (size location etc) for glass filled materials?
-
10th March 2020, 06:02 PM
#8
Re: 20% GF PP Warp
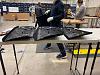
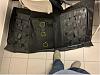
Sorry Rick- This is the valve gated part. the center pc is the one that is having all the warp. I have tried sequencing them, different pack times, starting to fill this panel first and last. 20% TF TPO meets all customer requirements and produces a flat part... Also better in my opinion all the way around in regards to wear on the machine and tooling.
Any advice would be appreciated.
Posting Permissions
- You may not post new threads
- You may not post replies
- You may not post attachments
- You may not edit your posts
-
Forum Rules