-
16th November 2018, 08:15 PM
#8
Re: Rubber Matt has Hazy Areas
Where is part gated?
That thing?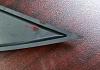
Definitely drying this material properly is critical - really any exposure to air for just a few minutes will absorb moisture and any cracks or air gaps in your dryer/feed system can be problematic.
(learned this the hard way).
Also working with this material I've experience better results filling on first stage - almost around 99.99999% full on first stage.
Reason is because once the material starts to slow down - it STOPS
Looking at your part I'm just imagining where the gate is, and how the flow-front would behave along part featues.
If you filled with one injection speed your flow-front would be Fast in areas with small cross section and Slow in areas with large cross section, which is bad for a material that wants to STOP when it slows down. This could cause the hazyness, maybe.
I'd recommend a shot size study and run fill-only parts at various transfer positions so you can visually see your flow-front at various stages and note any swirling/whirling that's going on. (10% full 20% full 30% full etc. etc.)
With this information you can do your best to 'profile' the injection to try to maintain the same flow-front rate across part features.
Steel surface finish also comes to mind..
Posting Permissions
- You may not post new threads
- You may not post replies
- You may not post attachments
- You may not edit your posts
-
Forum Rules